The AI Revolution: How CFOs Are Transforming Manufacturing's Future
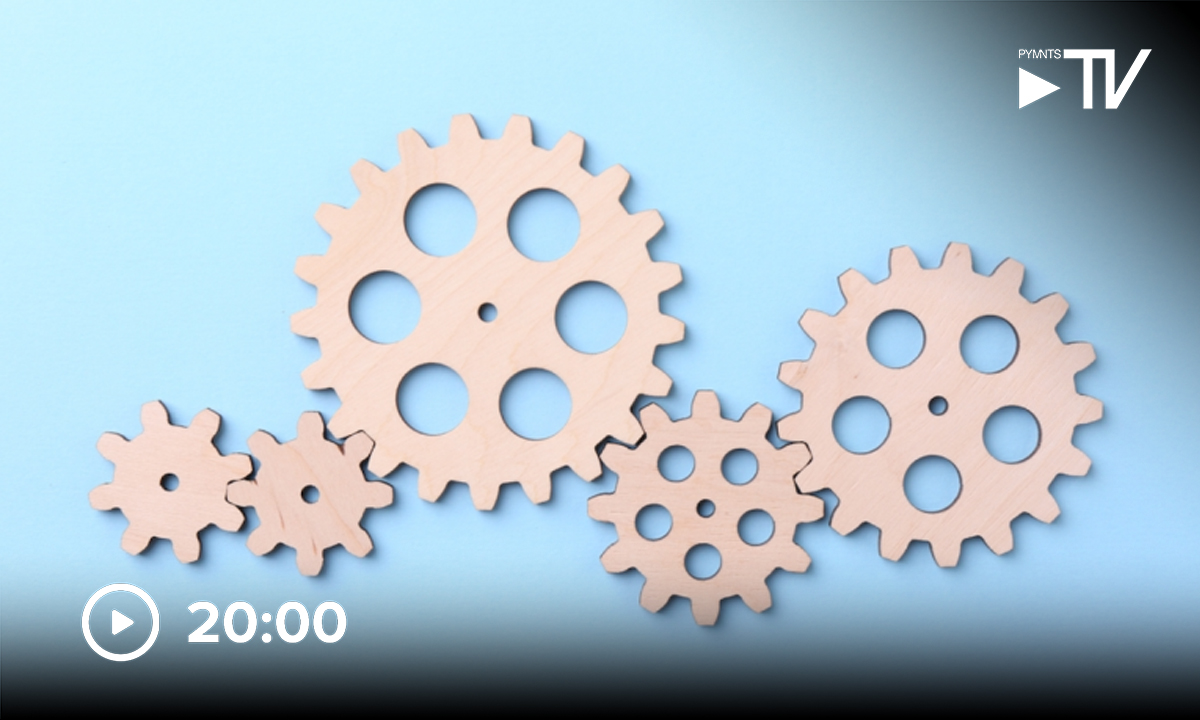
Do you remember floppy disks? Those tiny, fragile storage devices that once seemed cutting-edge? Surprisingly, some manufacturers are still clinging to technology that belongs in a museum. In today's fast-paced digital landscape, running a modern manufacturing business on outdated enterprise systems is like trying to win a Formula 1 race with a horse-drawn carriage.
The manufacturing world has evolved dramatically, yet some companies remain stubbornly anchored to legacy technologies that hinder innovation, efficiency, and competitiveness. These technological relics not only slow down operations but also create significant vulnerabilities in an increasingly interconnected and digital business environment.
It's time for manufacturers to embrace digital transformation, upgrade their systems, and step confidently into the 21st century. The future of manufacturing demands agility, real-time data processing, and seamless integration – something that outdated technologies simply cannot deliver.