Tech Revolution Stalled: Manufacturers Caught Between Innovation Dreams and Digital Roadblocks
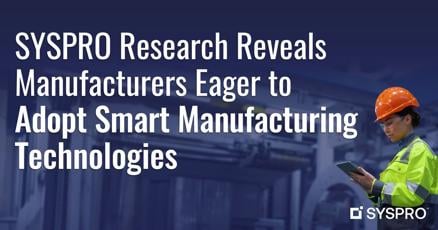
Manufacturing Faces Ongoing Challenge: Skilled Labor Shortage Continues to Strain Industry
The manufacturing sector is grappling with a persistent and critical issue: a significant shortage of skilled workers. Recent data underscore the depth of this challenge, revealing that finding and retaining qualified talent remains a top priority for manufacturers across the industry. This ongoing labor shortage threatens to impact production capabilities, innovation, and overall economic growth.
Companies are increasingly seeking innovative solutions to bridge the skills gap, including targeted training programs, partnerships with technical schools, and competitive recruitment strategies. The demand for highly skilled workers with specialized technical expertise continues to outpace the available workforce, creating a complex challenge for manufacturers striving to maintain competitive edge and operational efficiency.