Survival Mode: Manufacturing's High-Wire Act in an Era of Perpetual Disruption
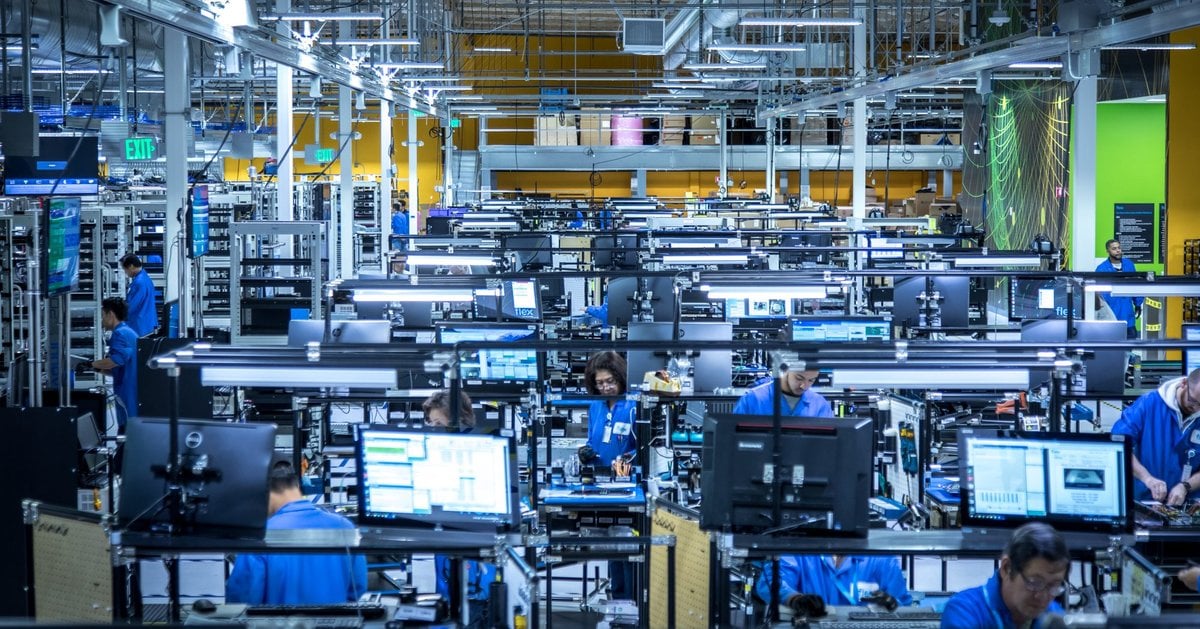
In today's volatile global marketplace, manufacturers face unprecedented challenges in navigating supply chain disruptions while simultaneously driving innovation. Paul Baldassari, President of Manufacturing & Services at Flex, offers critical insights into how companies can successfully adapt and thrive in this complex environment.
Supply chain resilience has become more than just a buzzword—it's a strategic imperative. Baldassari emphasizes that manufacturers must develop agile, flexible strategies that can quickly respond to unexpected global events, from pandemic-related shutdowns to geopolitical tensions.
Key to maintaining momentum is a multi-faceted approach that combines strategic planning, technological integration, and collaborative partnerships. By leveraging advanced digital technologies, companies can create more transparent and responsive supply chain networks that can rapidly pivot when disruptions occur.
Innovation cannot be put on hold during challenging times. Instead, manufacturers should view disruption as an opportunity to reimagine their processes, invest in cutting-edge technologies, and develop more robust, adaptable production models.
Flex's approach demonstrates that proactive planning, technological innovation, and strategic flexibility are the cornerstones of successfully managing supply chain complexity in an increasingly unpredictable global landscape.