Smart Machines, Smarter Manufacturing: How AI is Revolutionizing Factory Floors
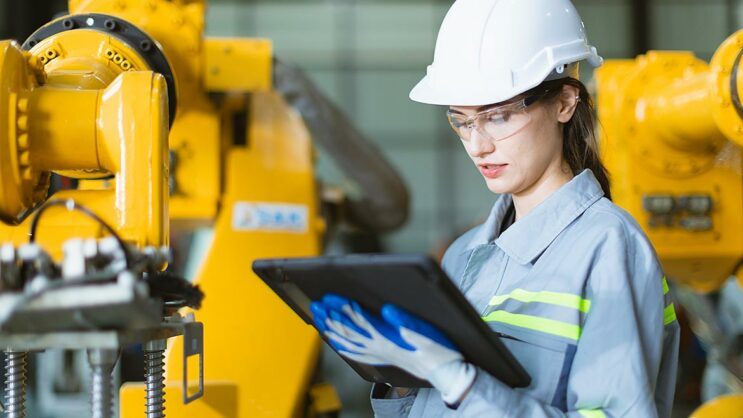
Revolutionizing Manufacturing: How AI Predicts and Prevents Machine Failures
In the fast-paced world of modern manufacturing, staying ahead means anticipating challenges before they arise. Enter AI-powered predictive maintenance—a game-changing technology that transforms how businesses approach equipment management.
By leveraging advanced algorithms and machine learning, this innovative approach allows companies to detect potential machine failures long before they occur. Instead of waiting for equipment to break down, manufacturers can now proactively schedule maintenance, dramatically reducing unexpected downtime and costly repairs.
The impact is profound. A recent Deloitte study reveals that an overwhelming 86% of manufacturing executives believe artificial intelligence and intelligent technologies will be critical in enhancing their competitive edge over the next five years. This isn't just a trend—it's a technological revolution that's reshaping industrial operations.
Predictive maintenance powered by AI doesn't just save time and money; it represents a fundamental shift in how businesses approach equipment management. By transforming reactive maintenance into a strategic, data-driven process, companies can optimize performance, extend machinery lifespans, and ultimately drive significant operational efficiencies.