Revolutionizing Manufacturing: Daimler Truck's 3D Printing Breakthrough Transforms Spare Parts Production
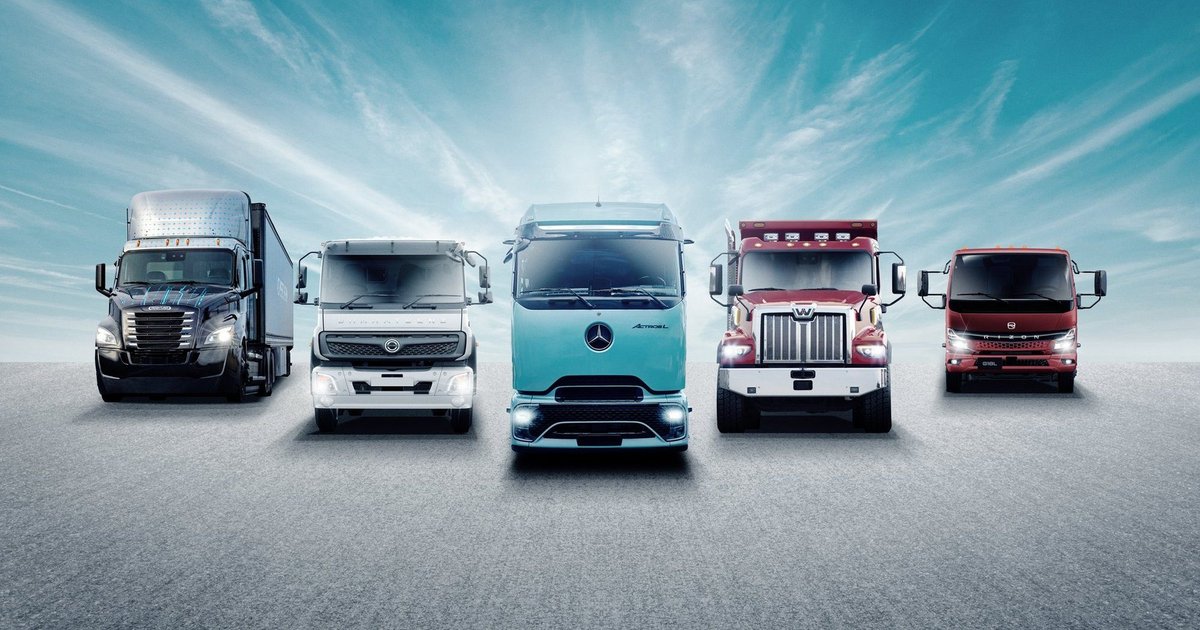
In a groundbreaking partnership, a leading automotive manufacturer has joined forces with 3D Systems to develop an innovative decentralized 3D printing solution. This cutting-edge collaboration is set to transform the landscape of spare part production, offering unprecedented flexibility and efficiency in the automotive industry.
By leveraging advanced 3D printing technology, the manufacturer aims to revolutionize traditional supply chain methods, enabling rapid, on-demand production of spare parts. This strategic approach not only reduces inventory costs but also dramatically shortens the time between part design and manufacturing.
The decentralized printing solution promises to streamline maintenance processes, providing automotive workshops and service centers with the ability to quickly produce high-quality replacement components directly at their locations. This breakthrough technology represents a significant leap forward in automotive parts management, potentially reducing downtime and improving overall customer service.