Revolutionary Hybrid Manufacturing Platform: Fusion Medusa Breaks Barriers in Large-Format Production
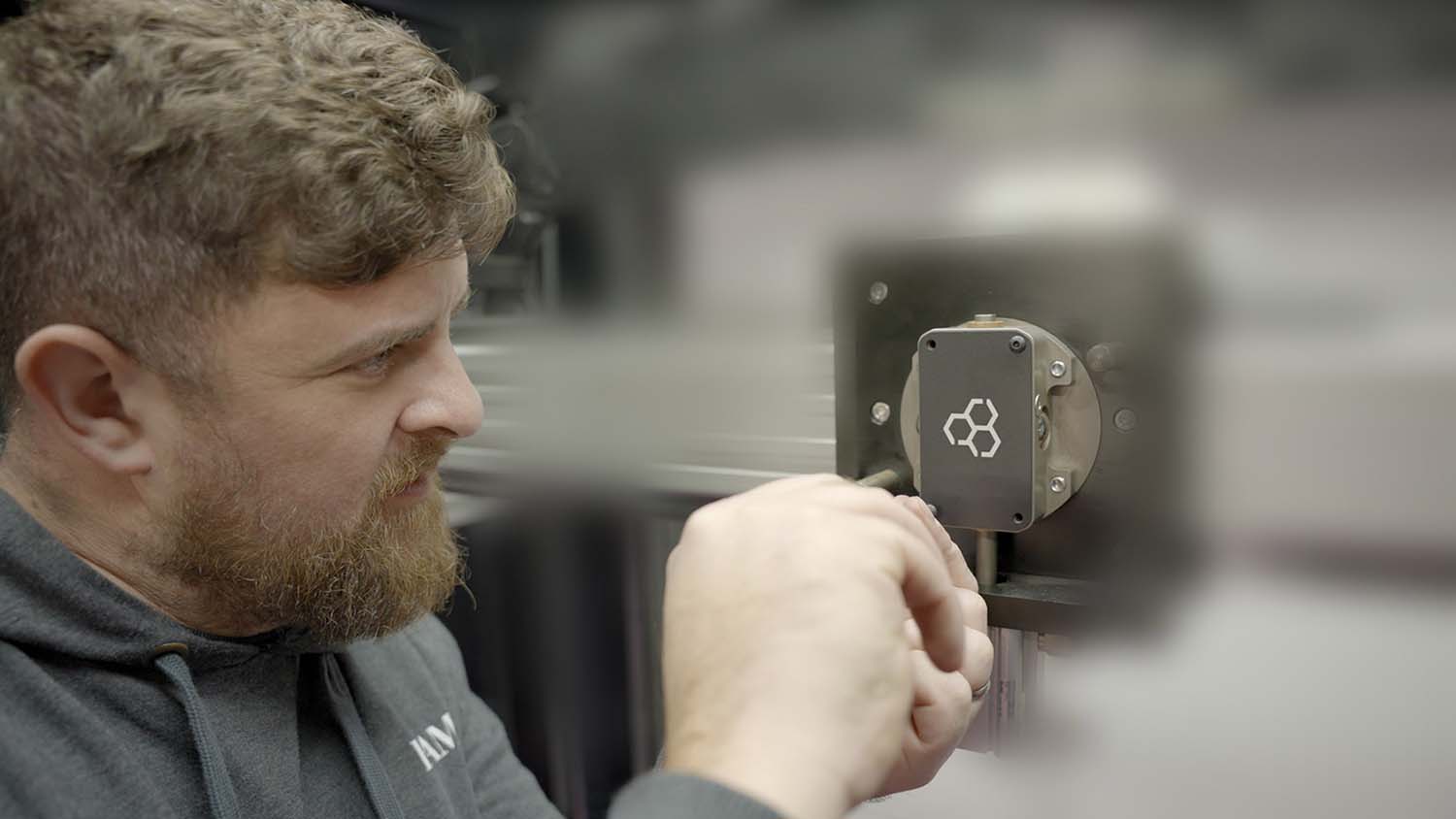
Introducing the Rapid Fusion Medusa: A Groundbreaking Hybrid 3D Printing Marvel from the UK
Engineering innovation has reached new heights with the Rapid Fusion Medusa, the first large-format hybrid 3D printer developed in the United Kingdom. This cutting-edge machine seamlessly integrates multiple advanced manufacturing technologies, including a pellet extruder, filament printing capabilities, and precision CNC machining tools.
The Medusa represents a significant leap forward in additive manufacturing, offering unprecedented versatility and flexibility for designers, engineers, and manufacturers. By combining different printing and machining techniques into a single, powerful platform, this revolutionary device enables users to create complex, high-precision components with remarkable efficiency.
With its ability to switch between pellet extrusion, filament printing, and CNC machining, the Rapid Fusion Medusa breaks traditional manufacturing limitations, providing a comprehensive solution for rapid prototyping, custom fabrication, and advanced manufacturing applications.