Revolution in Pharmacy: 3D Printing Transforms Drug Manufacturing on the Spot
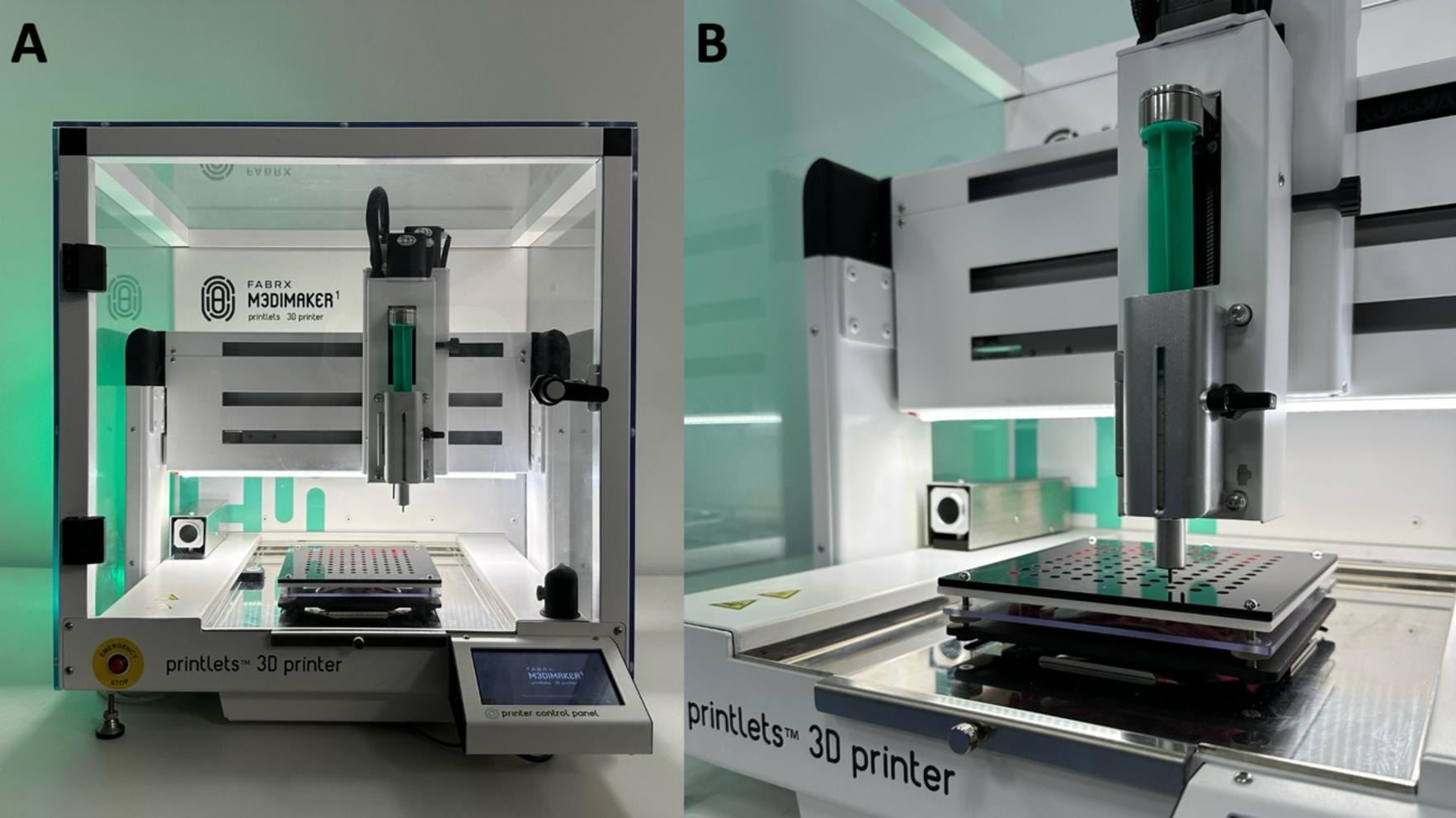
Revolutionizing Pharmaceutical Manufacturing: FABRX's M3DIMAKER 1 Transforms Capsule Production
In a groundbreaking leap forward for pharmaceutical technology, FABRX has unveiled its cutting-edge M3DIMAKER 1 3D printer, promising to reshape the landscape of capsule manufacturing. This innovative solution is set to dramatically enhance both production efficiency and patient safety in the pharmaceutical industry.
The M3DIMAKER 1 represents a quantum leap in precision drug delivery, offering pharmaceutical companies an unprecedented opportunity to streamline their manufacturing processes. By leveraging advanced 3D printing technology, the device enables unprecedented control over capsule design, composition, and dosage accuracy.
Key advantages of the M3DIMAKER 1 include:
• Rapid prototyping of complex medication formats
• Enhanced precision in drug dosing
• Reduced production time and costs
• Improved patient-specific medication customization
• Minimized human error in manufacturing
As the pharmaceutical industry continues to evolve, FABRX's M3DIMAKER 1 stands at the forefront of a technological revolution, promising to deliver more personalized, efficient, and safer medication solutions for patients worldwide.