Mixing Magic: The Ultimate Lab Solution for Coatings Pros Revealed!
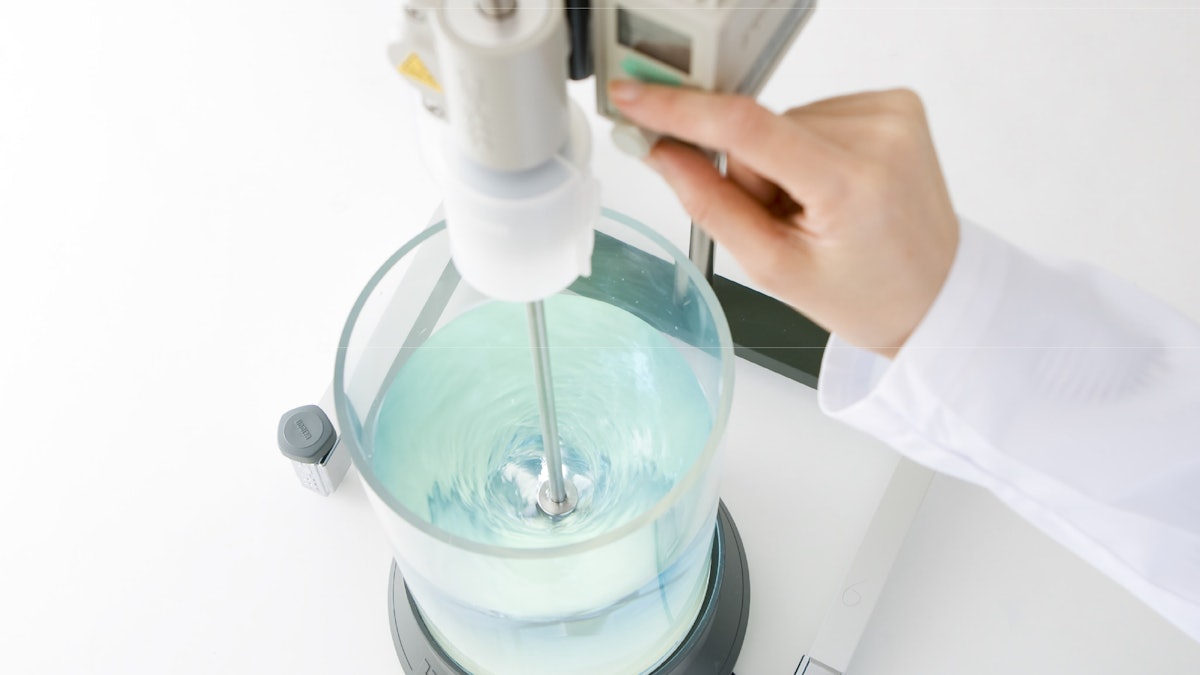
Navigating Equipment and Accessory Selection for Coatings Manufacturers
Selecting the right equipment and accessories is a critical decision for coatings manufacturers that can significantly impact product quality, production efficiency, and overall business success. This comprehensive guide explores the key considerations that manufacturers should evaluate when making equipment investments.
Critical Factors in Equipment Selection
Performance and Compatibility
Manufacturers must prioritize equipment that seamlessly integrates with existing production lines and meets specific coating application requirements. Compatibility ensures smooth workflow and minimizes potential disruptions in manufacturing processes.
Technological Innovation
Modern coating equipment should incorporate advanced technologies that enhance precision, reduce waste, and improve overall production capabilities. Look for innovations that offer real-time monitoring, automated controls, and adaptive manufacturing features.
Cost-Effectiveness
While initial investment is important, manufacturers should consider long-term value. This includes evaluating maintenance costs, energy efficiency, durability, and potential productivity gains that justify the equipment's price point.
Accessory Considerations
Quality and Reliability
Selecting high-quality accessories such as spray guns, pumps, and filtration systems is crucial. These components directly influence coating consistency, application accuracy, and final product performance.
Maintenance and Support
Choose equipment and accessories from manufacturers offering comprehensive technical support, readily available replacement parts, and robust warranty programs. This ensures minimal downtime and long-term operational reliability.
Strategic Decision-Making
Successful equipment selection requires a holistic approach that balances technical specifications, budget constraints, and future growth potential. Manufacturers should conduct thorough research, consult industry experts, and potentially test equipment before making significant investments.
Conclusion
By carefully evaluating performance, technological capabilities, cost-effectiveness, and support infrastructure, coatings manufacturers can make informed decisions that drive operational excellence and competitive advantage.