Manufacturing's Tech Maverick: Onkar Nerkar's Bold Vision for Industry 4.0 Revolution
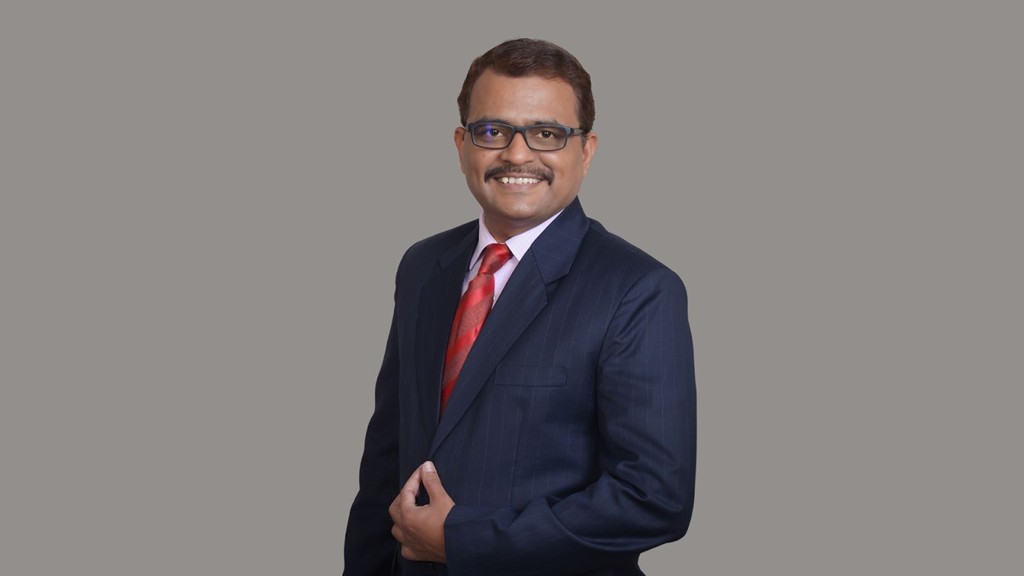
Digital technology is revolutionizing the manufacturing landscape, transforming traditional industrial processes into intelligent, interconnected systems. At the forefront of this technological revolution is Onkar Nerkar, a visionary director of continuous improvement and industrial engineering, who is turning the transformative potential of Industry 4.0 into concrete, game-changing innovations.
Nerkar's approach goes beyond mere technological implementation. He is strategically weaving together sustainability, operational resilience, and organizational agility to create manufacturing solutions that are not just technologically advanced, but also environmentally conscious and adaptable to rapidly changing market dynamics.
By leveraging cutting-edge digital technologies, Nerkar is helping manufacturers reimagine their operational frameworks, enabling them to respond more quickly to challenges, optimize resource utilization, and create more efficient, intelligent production ecosystems. His work represents a pivotal shift from traditional manufacturing models to a more dynamic, data-driven, and forward-thinking industrial paradigm.