Inside Manufacturing's Future: MAGNET Leader Reveals Industry Breakthrough at AU Summit
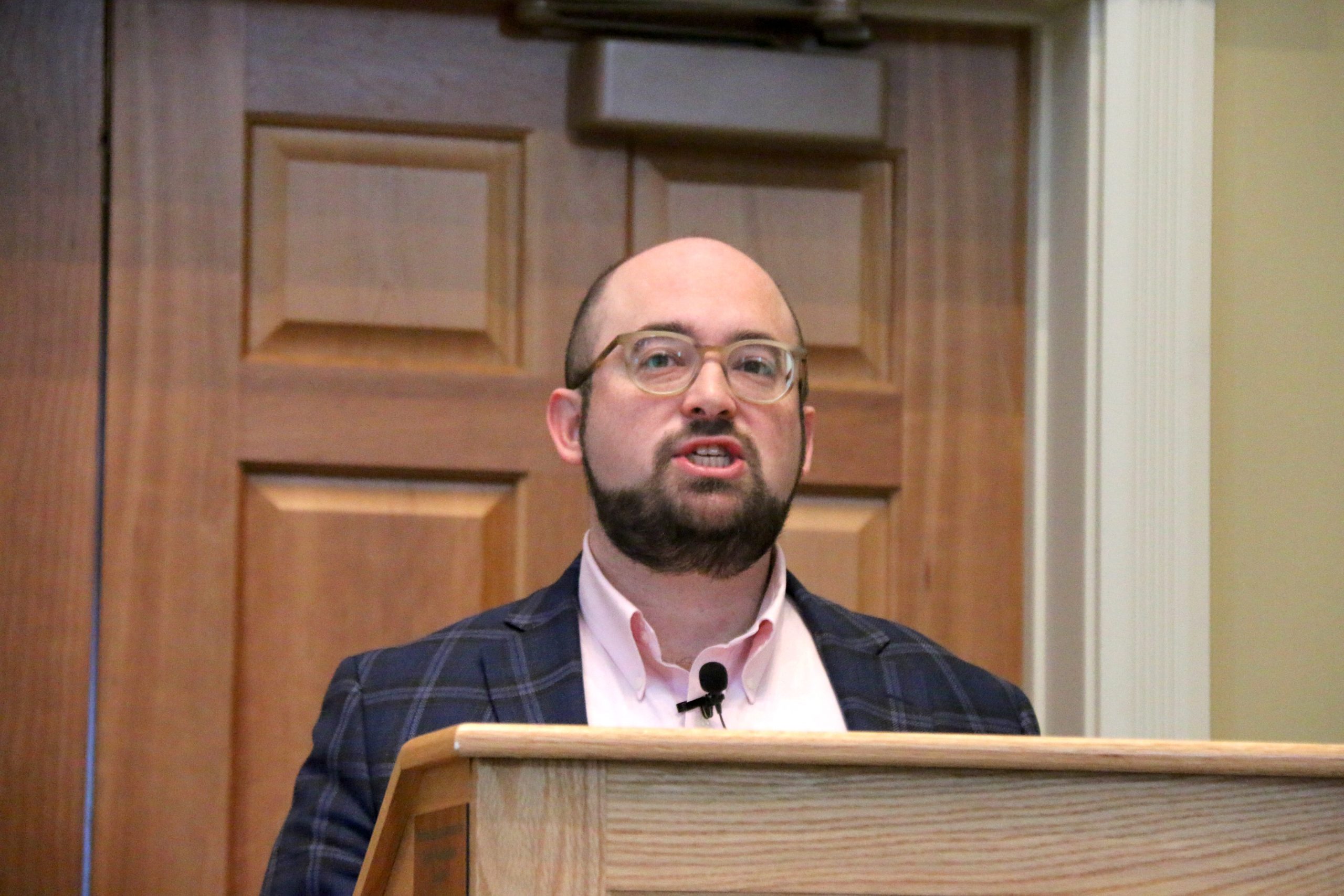
The COVID-19 pandemic has sent shockwaves through the manufacturing sector, creating an unprecedented journey of challenges and adaptations. Ethan Karp, CEO of The Manufacturing Advocacy and Growth Network (MAGNET), describes the industry's recent experience as a dramatic roller coaster ride, marked by intense volatility and rapid transformations.
Since the onset of the pandemic, manufacturers have navigated unprecedented disruptions, from supply chain breakdowns to workforce challenges, forcing them to reimagine traditional operational strategies. The industry has been compelled to embrace innovation, resilience, and agility like never before, turning potential obstacles into opportunities for reinvention and growth.
Karp's insights highlight the remarkable adaptability of manufacturers who have demonstrated extraordinary capacity to pivot, innovate, and survive in an increasingly unpredictable global economic landscape. The manufacturing sector's journey through the pandemic represents a testament to human ingenuity and industrial resilience.