Electrifying Ohio: Honda Pumps $1 Billion into EV Future
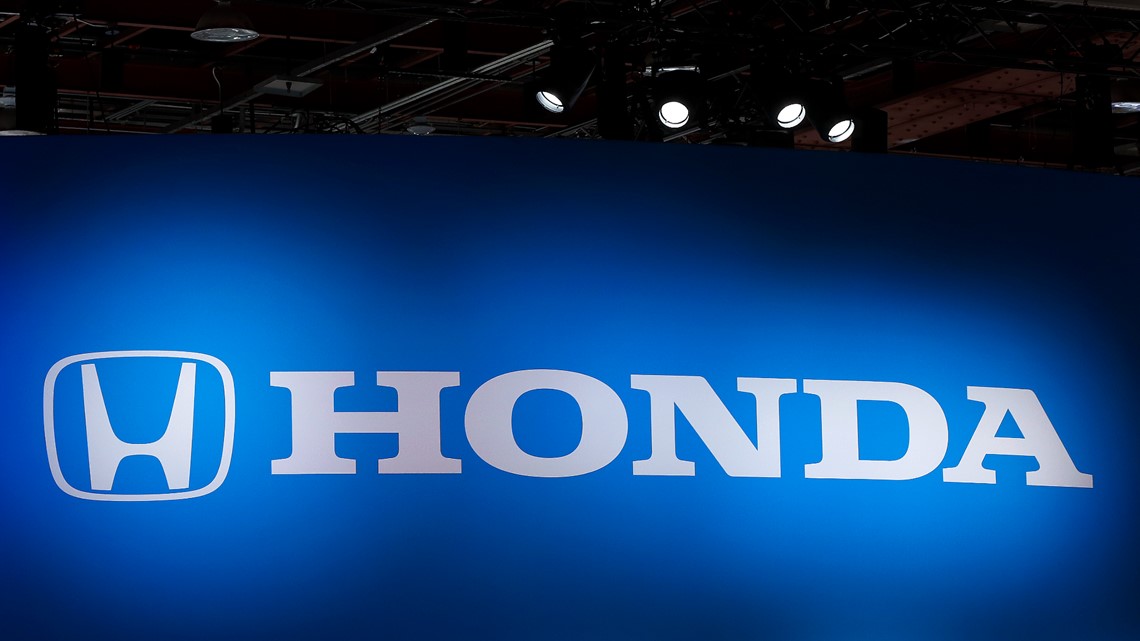
Revolutionary Manufacturing Flexibility: A Game-Changing Production Approach
In a groundbreaking move, the latest investment introduces a cutting-edge manufacturing system that represents the pinnacle of automotive production innovation. This advanced production line breaks traditional manufacturing barriers by enabling seamless production of internal combustion engine, hybrid, and battery-electric vehicles on the same assembly line.
The transformative technology allows manufacturers unprecedented flexibility, eliminating the need for separate production facilities for different vehicle types. By integrating multiple powertrain technologies into a single production environment, manufacturers can quickly adapt to changing market demands, reduce retooling costs, and streamline their manufacturing processes.
This adaptive manufacturing approach not only represents a significant technological achievement but also signals a new era of automotive production—one that embraces versatility, efficiency, and rapid technological evolution. As the automotive industry continues to transition towards electrification, such innovative manufacturing solutions will play a crucial role in helping automakers remain competitive and responsive to emerging market trends.