Breathing Innovation: BES Unveils Cutting-Edge Inhaler Production Hub with World-Class Clean Room Technology
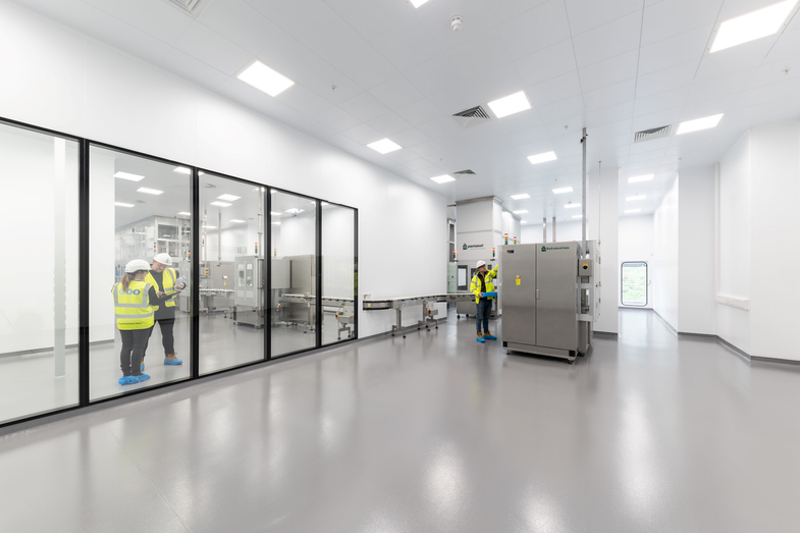
In a strategic move to advance its pharmaceutical manufacturing capabilities, Bespak, a leading Contract Development and Manufacturing Organization (CDMO), has selected a premier cleanroom design and construction specialist to develop its cutting-edge facility. The project will leverage state-of-the-art Building Information Modelling (BIM) technology and innovative modular construction techniques.
By partnering with this specialized design firm, Bespak demonstrates its commitment to creating a highly sophisticated and efficient pharmaceutical manufacturing environment. The use of BIM will ensure precise planning and visualization of the cleanroom facility, while modular construction promises enhanced speed, precision, and flexibility in the building process.
This forward-thinking approach highlights Bespak's dedication to implementing advanced technological solutions in pharmaceutical manufacturing infrastructure, setting a new standard for cleanroom facility development in the industry.